The Role of Vacuum Decay Tester in Quality Control for Packaging
Vacuum decay tester is a critical tool used in packaging and manufacturing to detect leaks, ensuring the integrity of products, especially in sensitive industries like food, pharmaceuticals, and electronics. The accuracy of a vacuum decay test can determine the durability of a package, preventing contamination and preserving product quality.
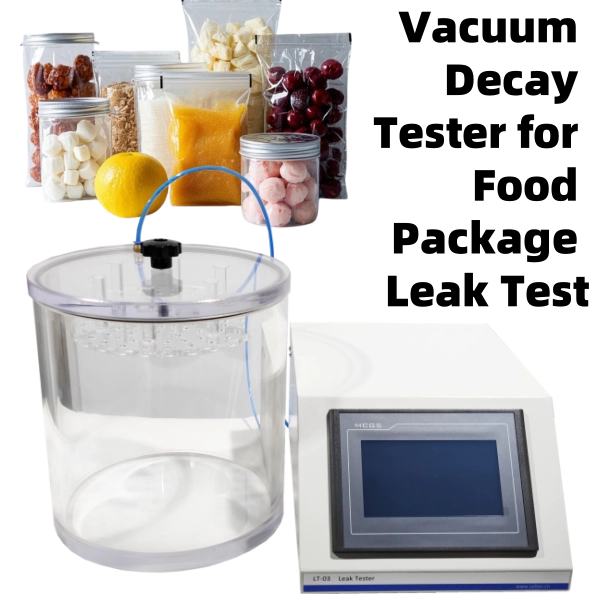
What is a Vacuum Decay Tester?
A vacuum decay tester is an instrument designed to detect leaks by measuring changes in pressure over time within a sealed package or container. It works by creating a vacuum inside the testing chamber, and if the package has any leaks, air will enter the chamber, causing a decay in the vacuum pressure. This process helps manufacturers identify defective packaging before products reach consumers. The vacuum decay tester is used to perform highly accurate tests on materials like plastic, glass, and metal packaging, making it an indispensable tool in industries that require high-quality packaging.
Vacuum Leak Detection: The Importance of Accurate Results
Vacuum leak detection is crucial for ensuring that products maintain their integrity and safety. Leaks in packaging can lead to contamination, spoilage, or loss of product quality, particularly in the food and pharmaceutical industries. A vacuum decay tester helps detect even the smallest leaks that may not be visible to the naked eye. By providing reliable results, manufacturers can prevent faulty products from reaching the market, thus reducing waste, enhancing consumer satisfaction, and complying with industry regulations.
Important for Food Package Leak Test
Food packaging must provide a reliable barrier against contaminants, moisture, and air to preserve the freshness and shelf-life of the product. The vacuum decay tester is essential for food package leak tests, ensuring that each package is sealed properly. Whether it’s for snack bags, beverage containers, or vacuum-sealed meat packages, this test helps guarantee that packaging meets industry standards. Testing packages using the vacuum decay tester can help identify issues such as pinholes, imperfect seals, or other defects that could compromise the food product’s quality or safety.
ASTM D3078: Standard for Vacuum Leak Detection
ASTM D3078 is a widely recognized standard that governs the procedure for performing vacuum decay tests on packages. This standard specifies the test conditions, equipment requirements, and acceptable limits for leak detection. By adhering to ASTM D3078, manufacturers can ensure their packaging meets global quality standards, which is particularly critical for products that require tamper-evident and airtight packaging. The ASTM D3078 standard outlines how the vacuum decay tester should be calibrated, how the test should be performed, and what constitutes a pass or fail result. Compliance with this standard helps maintain high levels of safety and quality across various industries.
Key Advantages of Using a Vacuum Decay Tester
- Enhanced Accuracy: The tester provides highly precise leak detection results, helping identify even the smallest imperfections in packaging.
- Kostnadseffektiv: Early detection of packaging defects prevents costly product recalls and reduces waste.
- Mångsidighet: It can be used to test a variety of packaging materials, including flexible pouches, bottles, and blister packs.
- Quick and Efficient Testing: The test provides rapid results, helping manufacturers meet production deadlines without compromising on quality.
- Efterlevnad: By following ASTM D3078 standards, manufacturers can ensure their packaging complies with international regulations and quality expectations
FAQs:
1. Can vacuum decay testers detect leaks in all types of packaging?
Yes, the tester can detect leaks in various packaging materials such as plastic, glass, and metal. They are versatile and can be used for a wide range of products, including food, pharmaceuticals, and electronics.
2. How does a vacuum decay tester work?
The tester creates a vacuum inside a sealed package. If there is a leak, the pressure inside the testing chamber will decay, signaling the presence of a defect.
3. How does vacuum decay testing compare to other leak detection methods?
Compared to methods like dye penetration or pressure decay, vacuum decay testing is more sensitive to small leaks and can detect defects that might not be visible in other tests.
4. Why is ASTM D3078 important for vacuum decay testing?
ASTM D3078 provides a standardized methodology for performing vacuum decay tests, ensuring consistency and reliability in test results, which is essential for regulatory compliance and quality control.