შესავალი
Ensuring the integrity of plastic packaging is a critical concern for professionals in fields like packaging R&D, quality assurance, and material innovation. A compromised package can result in contamination, reduced shelf life, and customer dissatisfaction. Enter bubble leak testing—a reliable and straightforward method to identify leaks in packaging.
This guide explores the bubble leak test method in detail, touching on key aspects such as ASTM standards, procedures, solutions, and equipment. We’ll also introduce you to advanced tools like the Cell Instruments GLT-01 მთლიანი გაჟონვის ტესტერი, designed for precision testing. Whether you’re a packaging R&D manager or a material scientist, this guide is your comprehensive resource for mastering bubble leak testing.
1. What is Bubble Leak Testing?
Definition and Importance
Bubble leak testing is a destructive method used to detect leaks in packaging by submerging it in a solution and applying internal air pressure. Leaks are identified by the presence of escaping bubbles, which indicate a breach in the packaging material.
Applications in Packaging
This method is widely used in industries where packaging integrity is paramount, including:
- Food Packaging: Ensures products remain fresh and uncontaminated.
- Pharmaceuticals: Protects drugs and medical devices from external contamination.
- Consumer Goods: Maintains quality and extends product shelf life.
Relevance to ASTM Standards
ASTM standards, such as ASTM F2096, provide detailed guidelines for performing bubble leak tests. Adhering to these standards ensures that testing methods are reliable, repeatable, and recognized by regulatory bodies.
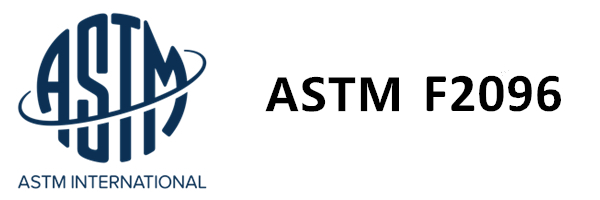
2. How Does the Bubble Leak Test Method Work?
Step-by-Step Explanation
Performing a bubble leak test involves the following steps:
- Sample Preparation: Select the packaging to be tested and ensure it is clean and free of debris.
- Setup: Fill the packaging with air or gas and seal it.
- Submersion: Immerse the packaging in a solution, typically water or a soap-based liquid.
- Pressurization: Apply internal pressure using equipment like the GLT-01 gross leak tester.
- Observation: Look for bubbles escaping from the packaging, indicating a leak.
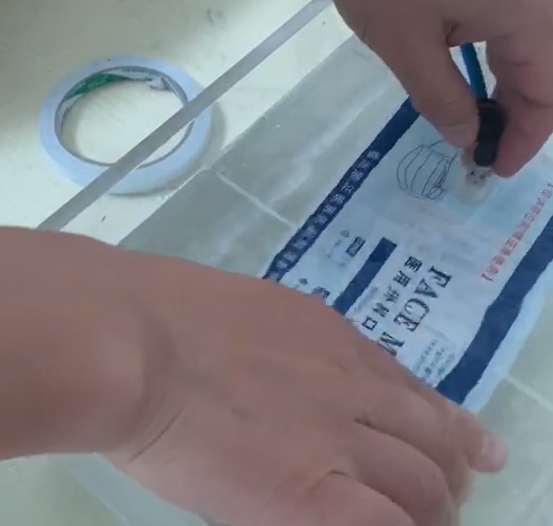
Required Equipment
Successful testing relies on the right tools. The Cell Instruments GLT-01 Gross Leak Tester offers precision control over pressure and observation, making it a go-to choice for professionals.
Common Test Solutions
The test solution plays a crucial role in detecting leaks. Commonly used solutions include:
- Plain Water: Ideal for small leaks.
- Soap Solutions: Enhance bubble visibility and detection accuracy.
Key Advantages
- Ease of Use: Simple and quick to set up.
- Cost-Effective: Minimal equipment and consumables required.
- Reliable: Accurate identification of leaks, ensuring packaging integrity.
3. Understanding ASTM Standards for Bubble Leak Testing
Overview of ASTM F2096 and Related Standards
ASTM F2096 is the primary standard governing bubble leak testing. It provides a clear framework for the method, including pressure requirements and observation criteria. Other relevant standards include: ASTM D3078, ASTM F2054, ASTM F1140, ASTM F88
Why ASTM Compliance Matters
Adhering to ASTM standards ensures that your testing process is:
- Reliable: Delivers consistent results.
- Regulatory-Friendly: Meets global quality requirements.
- Credible: Establishes trust with stakeholders and customers.
Common Challenges and Solutions
- Challenge: Misinterpreting bubble presence due to solution turbulence.
- Solution: Use precise equipment like the GLT-01 to control pressure accurately.
- Challenge: Difficulty in identifying micro-leaks.
- Solution: Utilize soap-based solutions to improve bubble visibility.
- Challenge: Creating air inflation hole.
- Solution: Utilize a needle-like object to puncture the sample and seal it with a cushion or tape that attaches to the air probe.
4. Choosing the Right Bubble Leak Test Equipment

Features of High-Quality Equipment
When selecting equipment, look for these key features:
- Pressure Control: Enables accurate testing.
- Durability: Long-lasting and long service life
- Compliance: Meets ASTM standards like F2096.
- User-Friendliness: The program needs to be easy to operate to enable an efficient and quick test process.
Spotlight on the GLT-01 Gross Leak Tester
The Cell Instruments GLT-01 Gross Leak Tester stands out for its:
- Precision: Accurate pressure application for consistent results.
- Ease of Use: Intuitive interface for seamless operation.
- Versatility: Suitable for a variety of packaging types and materials.
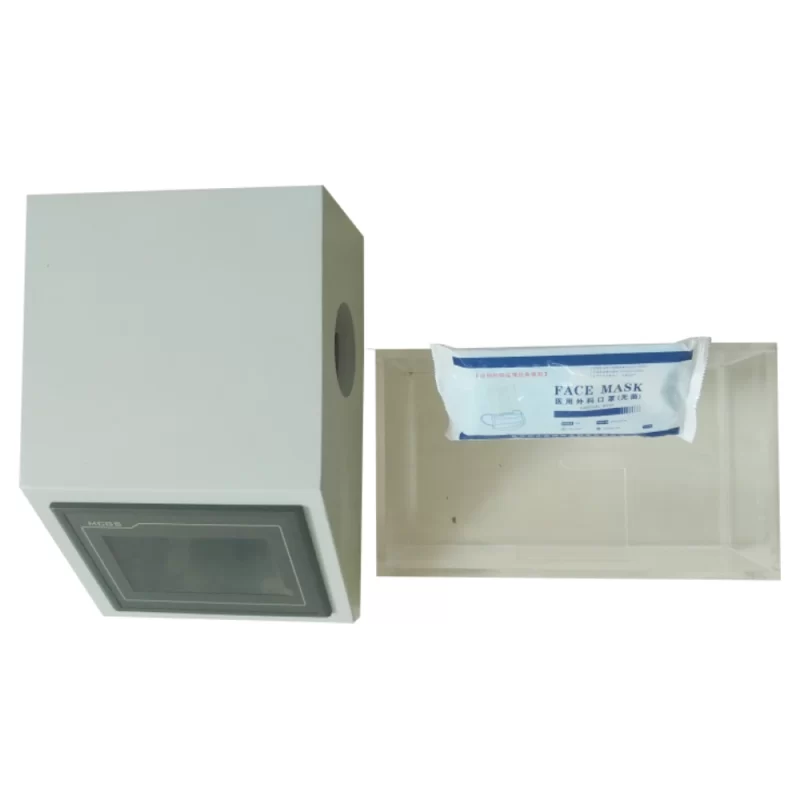
Comparison with Other Equipment
Compared to manual methods or less advanced testers, the GLT-01 offers superior accuracy, user-friendliness, and compliance with industry standards, making it an essential tool for professionals.
5. Best Practices for Conducting Bubble Leak Tests
Optimizing Test Conditions
- Temperature Control: Ensure the test solution is at room temperature to avoid errors.
- Proper Sealing: Verify that the packaging is sealed correctly before testing.
Common Errors to Avoid
- Over-pressurization: Can damage the packaging and yield false results.
- Insufficient Observation Time: Allow adequate time to detect slower leaks.
Maintaining Equipment
- Regular Calibration: Keep your equipment calibrated for accuracy.
- Routine Cleaning: Prevent contamination of the test solution.
- Periodic Inspections: Check for wear and tear to ensure consistent performance.
Conclusion
Bubble leak testing is a cornerstone of quality assurance for plastic packaging. It provides a reliable way to detect leaks, ensuring product integrity and customer satisfaction. By adhering to ASTM standards and using advanced tools like the Cell Instruments GLT-01 Gross Leak Tester, professionals can streamline their testing processes and achieve precise results.
If you’re looking to enhance your packaging testing capabilities, contact us to learn more about the GLT-01 and how it can revolutionize your quality assurance efforts.